1. 傳統(tǒng)技術(shù) 軸套、導(dǎo)套等作往復(fù)運(yùn)動(dòng)的機(jī)械零部件,因合金摩擦系數(shù)高容易導(dǎo)致磨損失效,傳統(tǒng)的自潤滑工藝主要是鑲嵌石墨(圖1)、多孔貯油技術(shù)(圖2)。但此類軸承存在以下缺點(diǎn):1)軸套表面打孔降低了承載能力;2)潤滑僅在孔及其周邊區(qū)域;3)鑲嵌的潤滑物多為單一的石墨或MoS2,潤滑性能有限,而復(fù)合潤滑物制備工藝又比較復(fù)雜。 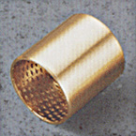
圖1 打孔鑲嵌潤滑物技術(shù) 圖2 打孔貯油軸套 2. 噴涂技術(shù) 目前日本大同工業(yè)精密株式會(huì)(圖3)、美國輝門(圖4)、歐洲米巴(5)等集團(tuán)采用的是多聚物噴涂技術(shù)。 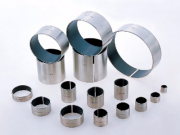
圖3大同軸套(內(nèi)表面) 圖4輝門軸套(內(nèi)表面) 圖5米巴軸套(內(nèi)表面) 由于PVD磁控濺射技術(shù)涂層沉積效率低、涂層材料靶材利用率一般不超過40%,且尺寸較大的機(jī)械零部件難以沉積涂層(設(shè)備尺寸限制),雖然多聚物涂層性能不及PVD涂層,但已有的研究表明,多聚物涂層干摩擦系數(shù)低于0.1,疲勞承載能力大于90MPa。國外多聚物涂層在啟停10萬次后,磨損降低674.35%[1] 。(Uehara S., Costa S.M.C., Da Silva Pra?a M.S., Dos S.F.M., New polymeric coated engine bearings for marginal lubrication conditions [J], 2011, 36:0189.) 由上海交通大學(xué)優(yōu)秀博士曹均研制的多聚物涂層技術(shù),如圖6所示,該軸套經(jīng)過測(cè)試具有以下特征:1)干摩擦系數(shù)0.10;2)使用溫度-30至220℃;3)承載能力超過85MPa;4)表面粗糙度Ra小于0.8微米;5)涂層表面均勻性小于±3μm。
圖6 銅合金軸套(內(nèi)表面) 3. 試驗(yàn)測(cè)試 由于曲面測(cè)試不方便,此次試驗(yàn)以面試驗(yàn)為考察目標(biāo),對(duì)涂層干摩擦性能進(jìn)行測(cè)試。 利用Rtec平面摩擦磨損試驗(yàn)機(jī)考核不同厚度涂層的摩擦磨損性能,首先根據(jù)涂料噴涂工藝對(duì)平面試樣進(jìn)行超聲清洗除油、平面噴砂處理和預(yù)熱處理,然后在相同條件下制備自潤滑涂層,如圖7所示,對(duì)制備的3種涂層厚度為6±2 μm,12±2 μm和24±2 μm的試樣分別標(biāo)記為A1, A2和A3。圖示可見,涂層表面光滑平整,且隨著涂層厚度的增加涂層顏色也越深。 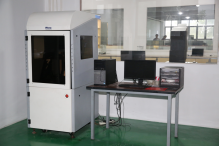
圖 7三種不同厚度涂層試樣 對(duì)涂層進(jìn)行平面摩擦磨損試驗(yàn),每種涂層進(jìn)行三次試驗(yàn)取平均值,試驗(yàn)參數(shù)如表1所示。測(cè)得不同涂層厚度的涂層摩擦系數(shù)曲線如圖8所示。不同厚度的平均摩擦系數(shù)關(guān)系為A2,即隨著涂層厚度的增加,摩擦系數(shù)呈先降低后增大趨勢(shì),涂層厚度為12±2 μm的摩擦系數(shù)最低。 表1 涂層摩擦試驗(yàn)參數(shù) 載荷 滑動(dòng)速度 時(shí)間 試驗(yàn)環(huán)境 對(duì)磨副 376.8N 300 r/min 10 min 25/200 ℃ ?4 mm鋼銷
圖 8三種不同厚度涂層摩擦系數(shù)
圖9三種不同厚度涂層磨痕 經(jīng)過摩擦試驗(yàn)后,三種不同厚度的涂層摩擦接觸磨痕如圖9所示。隨著涂層厚度的增加,在相同條件摩擦工況下的摩擦磨痕與涂層厚度成正比關(guān)系。24±2 μm厚度的涂層磨痕約1.5倍大小于12±2 μm厚度的涂層磨痕。觀察發(fā)現(xiàn)厚度為6±2 μm的涂層磨痕出現(xiàn)涂層磨破情況,涂層破裂為細(xì)小的溝狀。說明涂層越薄涂層越不耐磨。在與硬質(zhì)摩擦副摩擦工作時(shí)軟涂層越薄,其抵抗變形能力越差,涂層越容易被撕裂破損。A1涂層的摩擦系數(shù)從第5分鐘開始逐漸上升,說明在第5分鐘涂層開始撕裂破損。
圖10 三種不同厚度涂層摩擦阻礙 如圖10所示為不同厚度涂層在摩擦接觸過程中的摩擦阻礙示意圖,當(dāng)軟涂層與硬質(zhì)的對(duì)磨副接觸時(shí),軟涂層在接觸面受到接觸壓力作用變形。涂層越厚,摩擦副周邊的軟涂層變形越大,在摩擦副運(yùn)動(dòng)前進(jìn)方向涂層阻礙變形越大,因此24±2 μm厚的涂層磨痕比其他兩種厚度涂層的磨痕面積大。由于涂層變形和在摩擦副前進(jìn)方向的阻礙隨軟涂層的厚度增大,因此24±2 μm厚的涂層的摩擦系數(shù)高于12±2 μm涂層的摩擦系數(shù)。 對(duì)軸瓦進(jìn)行涂層結(jié)合強(qiáng)度測(cè)試,首先在軸瓦中央厚度區(qū)域、兩邊的45度區(qū)域進(jìn)行劃格,對(duì)軸瓦進(jìn)行水煮再粘貼撕拉試驗(yàn)(圖11),水開后持續(xù)15分鐘。對(duì)其他軸瓦進(jìn)行油煮再粘貼撕拉試驗(yàn)(圖12),油溫加熱到150℃,持續(xù)15分鐘,清洗除油后再撕拉試驗(yàn)。油牌號(hào)為10w-40。 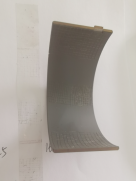
水煮結(jié)合強(qiáng)度測(cè)試(圖11) 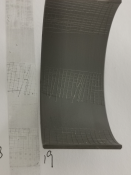
油煮結(jié)合強(qiáng)度測(cè)試(圖12) 進(jìn)一步進(jìn)行彎曲結(jié)合強(qiáng)度測(cè)試,結(jié)果如圖13所示: 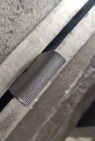
圖13 軸瓦彎曲涂層結(jié)合強(qiáng)度測(cè)試 無論是水煮、油煮還是彎曲測(cè)試,軸瓦涂層均未發(fā)生脫落。 4. 裝機(jī)測(cè)試 對(duì)軸瓦進(jìn)行裝機(jī)測(cè)試,轉(zhuǎn)速為3000r/min,負(fù)載30MPa。試驗(yàn)機(jī)如圖14所示,試驗(yàn)結(jié)果如圖15所示。
圖14 裝機(jī)測(cè)試 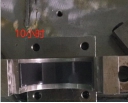 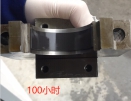 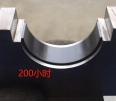
圖15 300小時(shí)裝機(jī)結(jié)果 裝機(jī)結(jié)果表明涂層性能良好。 5. 總結(jié) [1] 相對(duì)于鑲嵌技術(shù)和電鍍技術(shù),多聚物涂層技術(shù)無論是自潤滑性,還是承載能力都具有優(yōu)勢(shì),雖然性能不及PVD技術(shù),但噴涂工藝簡(jiǎn)單、生產(chǎn)效率高、價(jià)格便宜。 [2] 現(xiàn)有涂層疲勞強(qiáng)度超過85MPa,可滿足多數(shù)工況使用要求,涂層主要是由改性樹脂和納米潤滑及陶瓷耐磨材料組成,具有良好的潛藏性。 [3] 涂層具有良好的自潤滑性能,且長期在220℃溫況下服役。 [4] 多聚物涂層可以提高啟停摩擦磨損性能,能夠承受短期在無油工況服役,且提高在無油的干摩擦工況壽命。 [5] 涂層無論是水煮、油煮還是彎曲工況測(cè)試,涂層都沒有剝落現(xiàn)象,結(jié)合強(qiáng)度滿足使用要求。 [6] 裝機(jī)測(cè)試表明軸瓦具有良好的潤滑和耐磨功能,300小時(shí)測(cè)試涂層無明顯磨損變化特征出現(xiàn)。 [7] 涂層具有良好的潤滑耐磨性能,主要是提高啟停階段貧油潤滑甚至無油干摩擦工況,但長期服役仍建議在油潤滑工況下使用。
|